Gestión de Almacenes
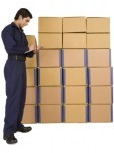
El concepto de almacén ha ido variando y ampliando su ámbito de responsabilidad. El almacén es una unidad de servicio y soporte en la estructura orgánica y funcional de una empresa comercial o industrial con objetivos bien definidos de resguardo, custodia, control y abastecimiento de materiales y productos. Hoy por hoy lo que antes se caracterizaba como un espacio dentro de la organización que tenía el piso de hormigón, es una estructura clave que provee elementos físicos y funcionales capaces de generar valor agregado.
¿Qué es la gestión de almacenes?
La gestión de almacenes se define como el proceso de la función logística que trata la recepción, almacenamiento y movimiento dentro de un mismo almacén hasta el punto de consumo de cualquier material – materias primas, semielaborados, terminados, así como el tratamiento e información de los datos generados. La gestión de almacenes tiene como objetivo optimizar un área logística funcional que actúa en dos etapas de flujo como lo son el abastecimiento y la distribución física, constituyendo por ende la gestión de una de las actividades más importantes para el funcionamiento de una organización.
El objetivo general de una gestión de almacenes consiste en garantizar el suministro continuo y oportuno de los materiales y medios de producción requeridos para asegurar los servicios de forma ininterrumpida y rítmica.
La Gestión de Almacenes se sitúa en el Mapa de Procesos Logísticos entre la Gestión de Existencias y el Proceso de Gestión de Pedidos y Distribución. De esta manera el ámbito de responsabilidad del área de almacenes nace en la recepción de la unidad física en las propias instalaciones y se extiende hasta el mantenimiento del mismo en las mejores condiciones para su posterior tratamiento.
El común interrogante que se genera luego de conocer los procesos del mapa logístico es: ¿Qué funciones corresponden a la Gestión de Inventarios (gestión de existencias) y que a la Gestión de Almacenes?. La siguiente gráfica despeja con exactitud el interrogante.
Importancia y objetivos de la gestión de almacenes
Describir la importancia y los objetivos de una gestión dependen directamente de los fundamentos y principios que enmarcan la razón de ser de la misma, sin embargo tal como lo observamos en la gráfica anterior sobre el "debe ser almacenado" quien formula las cuestiones de fundamento y principio es la gestión de inventario o existencia, y en estas se basa la gestión de almacenes para tener una gran importancia y unos claros objetivos.
Los objetivos que debe plantearse una gestión de almacenes son:
OBJETIVOS |
Rapidez de entregas |
Fiabilidad |
Reducción de costes |
Maximización del volumen disponible |
Minimización de las operaciones de manipulación y transporte |
y los beneficios (que justifican su importancia) son:
BENEFICIOS |
Reducción de tareas administrativas |
Agilidad del desarrollo del resto de procesos logísticos |
Optimización de la gestión del nivel de inversión del circulante |
Mejora de la calidad del producto |
Optimización de costes |
Reducción de tiempos de proceso |
Nivel de satisfacción del cliente |
Funciones del almacén
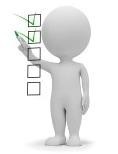
Aunque el derrotero de funciones de un almacén depende de la incidencia de múltiples factores tanto físicos como organizacionales, algunas funciones resultan comunes en cualquier entorno, dichas funciones comunes son:
- Recepción de Materiales.
- Registro de entradas y salidas del Almacén.
- Almacenamiento de materiales.
- Mantenimiento de materiales y de almacén.
- Despacho de materiales.
- Coordinación del almacén con los departamentos de control de inventarios y contabilidad.1
1TREJOS NOREÑA, Alexander. Gestión logística, Stocks, almacenes y bodegas.Seminarios Andinos.
Principios del almacén
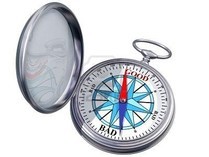
Como ya ha sido tratado en el módulo deAdministración de Inventarios, todo manejo y almacenamiento de materiales y productos es algo que eleva el costo del producto final sin agregarle valor, en teoría es un mal necesario, razón por la cual se debe conservar el mínimo de existencias con el mínimo de riesgo de faltantes y al menor costo posible de operación. Para llevar a cabo tal empresa, la gestión de almacenes debe establecer y regirse por unos principios comunes fundamentales, conocidos como principios del almacén (aplicables a cualquier entorno):
- La custodia fiel y eficiente de los materiales o productos debe encontrarse siempre bajo la responsabilidad de una solo persona en cada almacén.
- El personal de cada almacén debe ser asignado a funciones especializadas de recepción, almacenamiento, registro, revisión, despacho y ayuda en el control de inventarios.
- Debe existir un sola puerta, o en todo caso una de entrada y otra de salida (ambas con su debido control).
- Hay que llevar un registro al día de todas las entradas y salidas.
- Es necesario informar a control de inventarios y contabilidad todos los
movimientos del almacén (entradas y salidas), la programación y control de producción sobre las existencias. - Se debe asignar una identificación a cada producto y unificarla por el nombre común y conocido de compras, control de inventario y producción.
- La identificación debe estar codificada.
- Cada material o producto se tiene que ubicar según su clasificación e identificación en pasillos, estantes, espacios marcados para facilitar su ubicación. Esta misma localización debe marcarse en las tarjetas correspondientes de registro y control.
- Los inventarios físicos deben hacerse únicamente por un personal ajeno al almacén.
- Toda operación de entrada o salida del almacén requiriere documentación autorizada según sistemas existentes.
- La entrada al almacén debe estar prohibida a toda persona que no esté asignada a él, y estará restringida al personal autorizado por la gerencia o departamento de control de inventarios.
- La disposición del almacén deberá ser lo más flexible posible para poder realizar modificaciones pertinentes con mínima inversión.
- Los materiales almacenados deberá ser fáciles de ubicar.
- La disposición del almacén deberá facilitar el control de los materiales.
- El área ocupada por los pasillos respecto de la del total del almacenamiento propiamente dicho, debe ser tan pequeña como lo permitan las condiciones de operación.2
2TREJOS NOREÑA, Alexander. Gestión logística, Stocks, almacenes y bodegas.Seminarios Andinos.
Proceso de la gestión de almacenes
El mapa de proceso de la gestión de almacenes se compone de dos ejes transversales que representan los procesos principales - Planificación y Oraganización y Manejo de la información - y tres subprocesos que componen la gestión de actividades y que abarca la recepción, el almacén y el movimiento.
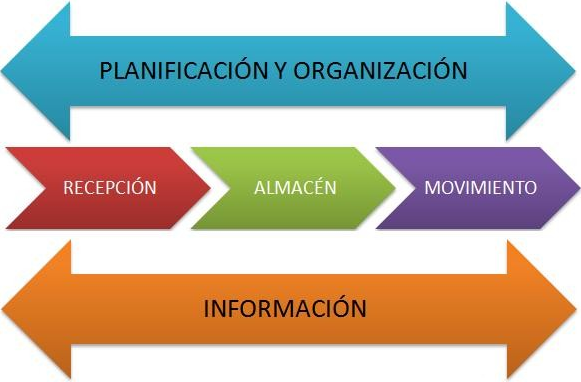
Planificación y Organización
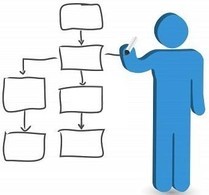
El proceso de planificación y organización es de carácter estratégico y táctico, dado que tiene que brindar soluciones de recursos en comunión con las políticas y objetivos generales que contempla la estrategia de la compañía, en aras de potenciar las ventajas competitivas por las que apuesta la misma. Dentro de las actividades o subprocesos que se deben realizar en el proceso de planificación y organización se encuentran:
- Diseño de la red de distribución de la compañía: Toda compañía necesita establecer políticas respecto a su red de distribución, dado que esta debe ser acorde a su mercado y óptima en capacidad de respuesta para mitigar las fluctuaciones de su demanda. La complejidad de las decisiones respecto al diseño de la red de distribución es tal, dado que requiere de la combinación precisa de instalaciones, modalidades de transporte, y estrategias. El Diseño de una Red de Distribución es la planificación y ubicación estratégica de los almacenes y centros de distribución de manera que permitan gestionar el flujo de productos desde uno o más orígenes hasta el cliente. Desarrollar una adecuada red de almacenes para la compañía y los clientes requiere considerar una cantidad significativa de elementos: Número de almacenes, las ubicaciones, la propiedad de la gestión o el tamaño de los mismos. Tras tener identificadas las necesidades de distribución y almacenamiento, la compañía debe decidir qué tipos de almacenes y centros de distribución se ajustan a sus necesidades de manera más eficiente, así como la ubicación de los mismos.
- Responsabilidades de la Gestión de Almacenes (Gestión Propia o Subcontratación): Una vez se ha diseñado la red de distribución se procede a determinar si se autogestionará el almacén o si se subcontratará. Una vez más la decisión depende de muchos factores dependientes de la estrategia de la organización, de su mercado, tamaño y cadena de abastecimiento, sin embargo existen claras ventajas y desventajas de acuerdo al tipo de gestión (propia o por subcontratación), dentro de las más significativas se encuentran:
Dado que regularmente para la determinación de la responsabilidad de la gestión se preponderan los argumentos financieros en un apartado posterior profundizaremos en métodos matemáticos que permitan establecer elementos cuantitativos de juicio para este subproceso de la planificación y organización.
- Ubicación de almacenes: La firma Pricewaterhousecoopers recomienda que la localización de los almacenes se aborde desde un enfoque con doble perspectiva:
- Una visión general del mercado: Para acotarse geograficamente a un área amplia, y
- Una visión local del mercado: Que contemple aspectos particulares de las zonas acotadas en la visión general.
Historicamente desde el plano de la Ingeniería Industrial se ha abordado el tema de la localización de almacenes mediante múltiples métodos matemáticos, entre los que se encuentran los métodos de: Von Thünen, Hoover, Weber, Greenhut y el método de Centro de Gravedad (Este último lo abordaremos desde el módulo de Diseño y Distribución en Planta). Sin embargo los factores no son meramente cuantitativos y existen una gran cantidad de criterios cualitativos (que evidentemente redundan en el plano financiero) y entre los que se destacan:
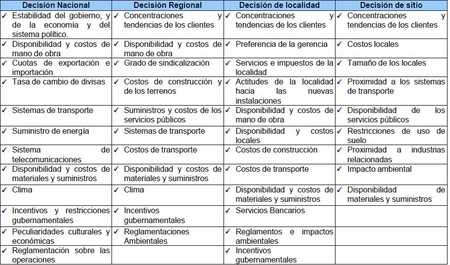
- Tamaño de los almacenes: Un almacén debe ser dimensionado principalmente en función de los productos a almacenar (en tamaño, características propias y cantidad de referencias) y la demanda (especialmente en sectores afectados por la estacionalidad de la demanda). Pero además de estos, intervienen otros factores que deben ser considerados a la hora de dimensionar el tamaño de un almacén. Los factores a tener en cuenta para el cálculo del tamaño de un almacén son:
- Productos a almacenar (cantidad y tamaños)
- Demanda de los mercados
- Niveles de Servicio al cliente
- Sistemas de manipulación y almacenaje a utilizar
- Tiempos de producción
- Economías de escala
- Lay out de existencias
- Requisitos de pasillos
- Oficinas necesarias
Es importante la consideración de las tres dimensiones para determinar la capacidad del almacén, es decir determinar la magnitud en función de metros cúbicos. En el módulo de Diseño, Tamaño y Lay-out de almacenes abordaremos matemáticamente el aspecto conocido como dimensionamiento de bodegas.
- Diseño y Lay-out de los almacenes: Una vez los tipos de almacenes y sus ubicaciones han sido definidos, se debe trabajar en conseguir el flujo de materiales más eficiente y efectivo dentro de los almacenes. En este sentido, un diseño efectivo optimiza las actividades de un almacén. En el módulo deDiseño, Tamaño y Lay-out de almacenes abordaremos este tema a profundidad.
Recepción
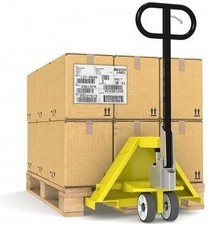
El flujo rápido del material que entra, para que esté libre de toda congestión o demora, requiere de la correcta planeación del área de recepción y de su óptima utilización. La recepción es el proceso de planificación de las entradas de unidades, descarga y verificación tal y como se solicitaron mediante la actualización de los registros de inventario.
El objetivo al que debe tender una empresa en su proceso de recepción de mercancías es la automatización tanto como sea posible para eliminar o minimizar burocracia e intervenciones humanas que no añaden valor al producto. Otra tendencia considerada como buena práctica logística es la implementación de programas de entregas certificadas que no solo eliminan burocracia sino que reducen al mínimo las inspecciones que se consideran imprescindibles pero que no añaden valor.
En primer lugar, el proceso de recepción de mercancías debe cimentarse en una previsión de entradas que informe de las recepciones a realizar en tiempo dado y que contenga, al menos, el horario, artículos, y procedencia de cada recepción, este proceso se conoce como cita previa ya que para procesos como Entregas Paletizadas se debe contar con recursos muy específicos como montacargas, plataformas moviles, rampas, entre otros.
Es evidentemente necesario que se distingan los ingresos de unidades internas de las externas. En el primero de los casos, los requerimientos de recepción son significativamente menores que las mercancías de origen externo, en el caso de que se realicen controles de procesos a lo largo de la vida de las mercancía.Además, una correcta metodología de identificaciones a lo largo de la compañía también favorece enormemente la actividad de recepción. Es el caso de traslado de mercancías entre almacenes o de proceso de transformación a almacén. Las mercancías de procedencia externa requieren unas condiciones de llegada más exhaustivas y deben haber sido establecidas previamente con el proveedor (cita previa - EDI), con lo que se precisa mayor actuación y responsabilidad desde el almacén.
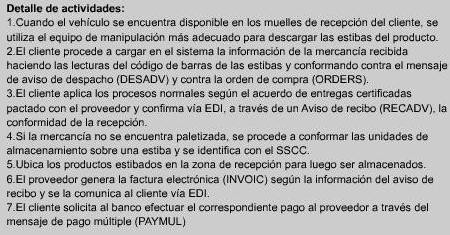
Tras la descarga e identificación, las cuales deben realizarse de manera inmediata y en zona específica habilitada a tal efecto, las mercancías deben pasar a almacenamiento, bien sea temporal a la espera de su ubicación definitiva, bien sea fijo en su ubicación definitiva.
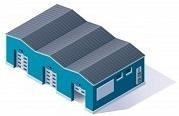
El almacenamiento o almacén es el subproceso operativo concerniente a la guarda y conservación de los productos con los mínimos riesgos para el producto, personas y compañía y optimizando el espacio físico del almacén. El almacén puede dividirse en las siguientes zonas:
ZONAS DE UN ALMACÉN |
Recepción: zona donde se realizan las actividades del proceso de recepción |
Almacenamiento, reserva o stock: zonas destino de los productos almacenados. De adaptación absoluta a las mercancías albergadas, incluye zonas específicas de stock para mercancías especiales, devoluciones, etc |
Preparación de pedidos o picking: zona donde son ubicados las mercancías tras pasar por la zona de almacenamiento, para ser preparadas para expedición |
Salida, verificación o consolidación: desde donde se produce la expedición y la inspección final de las mercancías |
Paso, maniobra: zonas destinadas al paso de personas y máquinas. Diseñados también para permitir la total maniobrabilidad de las
máquinas. Oficinas: zona destinada a la ubicación de puestos de trabajo auxiliares a las operaciones propias de almacén |
Oficinas: zona destinada a la ubicación de puestos de trabajo auxiliares a las operaciones propias de almacén |
Basado en: Pricewaterhousecoopers
Los Sistemas de Almacenamiento y Tipos de Almacén serán abordados en módulos independientes.
Movimiento
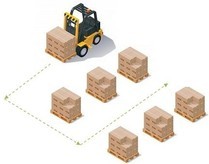
Es el subproceso del almacén de carácter operativo relativo al traslado de los materiales/productos de una zona a otra de un mismo almacén o desde la zona de recepción a la ubicación de almacenamiento. La actividad de mover físicamente mercancías se puede lograr por diferentes medios, utilizando una gran variedad de equipos de manipulación de materiales. El tipo de herramientas utilizado depende de una serie de factores como son:
- Volumen del almacén
- Volumen de las mercancías
- Vida de las mercancías
- Coste del equipo frente a la finalidad
- Cantidad de manipulaciones especiales y expediciones requeridas
- Distancia de los movimientos
Desde la perspectiva de las características de las mercancías, los flujos de entrada y salida del almacén de las mercancías son variadas, como por ejemplo:
- Last In – First Out (LIFO): la última mercancía que entra en almacén, es la primera que sale para expedición. Esta modalidad es frecuentemente utilizada en productos frescos.
- First In – First Out (FIFO): la primera mercancía que entra en almacén, es la primera que es sacada de almacén. Es la modalidad más utilizada para evitar las obsolescencias
- First Expired – First Out (FEFO): el de fecha más próxima de caducidad es el primero en salir.
Información
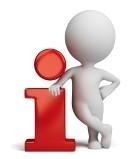
Si bien la función principal de la Gestión de Almacenes es la eficiencia y efectividad en el flujo físico, su consecución está a expensas del flujo de información, este es un eje transversal de los procesos de gestión logística, y la gestión de almacenes no son la excepción. Debe ser su optimización, por tanto, objetivo de primer orden en la Gestión de Almacenes. Su ámbito se extiende a todos los procesos anteriormente descritos – Planificación y organización, recepción, almacén y movimiento – y se desarrolla de manera paralela a ellos por tres vías:
- Información para gestión.
- Identificación de ubicaciones.
- Identificación y trazabilidad de mercancías.
Dentro de la información para la gestión se incluyen:
- Configuración del almacén: instalaciones, lay-out…
- Datos relativos a los medios disponibles
- Datos técnicos de las mercancías almacenadas
- Informes de actividad para Dirección
- Evolución de indicadores
- Procedimientos e instrucciones de trabajo
- Perfiles y requisitos de los puestos
- Registros de la actividad diaria
La identificación de las ubicaciones la profundizaremos en el módulo de Diseño y Lay-out de almacenes. Por otro lado la identificación y trazabilidad de mercancías se detalla en el módulo de identificación de mercancías.
INDICADORES DE DESEMPEÑO LOGÍSTICO - KPIs
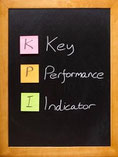
"Lo que no se puede medir no se puede controlar, lo que no se puede controlar no se puede administrar". La métrica es muy importante para el funcionamiento de una organización, dado que esta impacta directamente en la actitud y comportamiento de sus miembros, situándolos en un punto de evaluación respecto a los objetivos planteados y alcanzados. Hoy por hoy, se hacen necesarios métodos de evaluación que permitan la captura de información tanto cuantitativa
como cualitativa, dado que los sistemas métricos exclusivamente financieros no permiten determinar con certeza la magnitud y por ende no permiten potenciar las competencias y habilidades que se exigen a las organizaciones actuales, habilidades y competencias tales como logística, mejoramiento continuo e innovación y desarrollo.
Cuando se pretende iniciar un proceso de evaluación de la gestión logística de una organización, es imperativo extraer un conjunto de indicadores conocidos como KPI (Key Performence
Indicators), estos varían de acuerdo al proceso o a la actividad en consideración, y proporcionan una cuantificación del desempeño de la gestión logística y de la cadena de
abastecimiento.
¿QUÉ ES UN INDICADOR DE DESEMPEÑO LOGÍSTICO?
Los Indicadores de Desempeño Logístico son medidas de rendimiento cuantificables aplicados a la gestión logística que permiten evaluar el desempeño y el resultado en cada proceso de recepción, almacenamiento, inventarios, despachos, distribución, entregas, facturación y flujos de información entre las partes de la cadena logística. Es indispensable que toda empresa desarrolle habilidades alrededor del manejo de los indicadores de gestión logística, con el fin de poder utilizar la información resultante de manera oportuna (tomar decisiones).
CARACTERÍSTICAS DE LOS INDICADORES DE DESEMPEÑO LOGÍSTICO - KPIs
- Los KPIs logísticos deben de relacionarse con la misión, visión, estrategia corporativa y factores de competitividad de la organización.
- Los KPIs logísticos deben de enfocarse en el método para conseguir resultados, no tanto en los resultados mismos.
- Los KPIs logísticos deben de ser significativos y enfocados en la acción: de tal manera que los trabajadores puedan mejorar el resultado de los indicadores mediante su trabajo.
- Los KPIs logísticos deben ser coherentes y comparables, en la medida de lo posible deben ser estándar para permitir evaluaciones comparativas (benchmarking) entre diversas organizaciones.
MÉTODO DE CÁLCULO DE LOS INDICADORES DE DESEMPEÑO LOGÍSTICO
PLANIFICACIÓN DE LA CADENA DE ABASTECIMIENTO
ABASTECIMIENTO
Para efectuar el cálculo del Stock medio es frecuente sumar el Inventario Inicial y el Final y luego dividirlo entre dos (2).
TRANSPORTE
*Este indicador debe tenerse en cuenta solo si se dispone de flota de transporte propia
DISTRIBUCIÓN
GESTIÓN DE PEDIDOS
Entregas certificadas (véase Entregas Certificadas):
- Entregas completas.
- Fecha de entrega es igual a la estipulada por el cliente.
- La documentación que ampara la transacción es completa y exacta.
- Artículos en perfectas condiciones de calidad.
CADENA DE ABASTECIMIENTO
Además todos los indicadores logísticos pueden considerarse como indicadores de Cadena de Abastecimiento. Vale la pena aclarar que esta característica no es conmutativa, dado que la logística se encuentra contenida en la Gestión de la Cadena de Suministro. Véase Cadena de Abastecimiento y Logística
INCIDENCIA DE LOS KPIs LOGÍSTICOS EN LA MEJORA CONTINUA
El éxito de un proceso de mejora continua depende en gran medida de la solidez de su proceso de retroalimentación, es decir, la capacidad de ajustar lo necesario en marcha. Para ello es necesario contrastar los resultados proyectados con el actual progreso.
El proceso de retroalimentación en un proceso de mejora continua se genera desde la función de control y verificación, función que se divide en las siguientes acciones:
- Establecer estándares de desempeño
- Realizar el seguimiento del proceso actual
- Cotejar los resultados con los estándares establecidos
- Si existiesen variaciones, es necesario determinar las causas y efectuar las acciones correctivas.

Vale la pena aclarar que el proceso de mejora continua obtiene su movimiento de avanzada sobre la pendiente mediante la "Actuación" y la "Realización". Los estándares que se
generan desde la función de "Verificación" sirven de cuña para impedir que se genere un retroceso en el proceso, y a partir de estos estándares se apoyan las funciones
restantes.
Definir el layout del almacén es el primer paso en el trabajo de diseño de la instalación. La distribución del espacio es aparentemente una cuestión sencilla, pero resulta complicada de resolver en la práctica. En este artículo se definen los principales factores que es preciso considerar, así como un ejemplo de layout de almacén con una distribución en seis áreas diferenciadas.
Generalmente, el diseñador de un almacén se suele encontrar con un espacio en el que ciertos factores suponen una seria limitación sobre la superficie disponible. Es por ello que la distribución ha de ser cuidadosamente estudiada.
Cuando se ha de decidir la disposición que ha de tener un almacén, tanto interna como externa, pueden darse tres diferentes situaciones que pueden hacer necesaria una diferente asignación de espacios, como son la instalación de nuevos almacenes, la ampliación de los ya existentes o la reorganización de los que actualmente están en servicio.
La última de estas tres situaciones no implica, para su resolución, la necesidad de tomar decisiones de mucha trascendencia que afecten a medio y a largo plazo al desarrollo del negocio.
No obstante, cualquiera que sea la situación, la distribución general de una instalación debe ser acorde con un buen sistema de almacenamiento, que no es otro que aquel que cubre estas necesidades: el mejor aprovechamiento del espacio, la reducción al mínimo de la manipulación de las mercancías, la facilidad de acceso al producto almacenado, el máximo índice de rotación posible, la flexibilidad máxima para la colocación del producto y la facilidad de control de las cantidades almacenadas.
Para conseguir esos objetivos, primero se ha de efectuar una distribución planimétrica, lo que se conoce más habitualmente con el término inglés lay-out, es decir, el diseño de un almacén plasmado en un plano.
El lay-out debe realizarse respetando, ante todo, las reglas básicas del buen almacenamiento que se han citado, además de evitar zonas y puntos de congestión, facilitar las tareas de mantenimiento y determinar los medios necesarios para obtener la mayor velocidad de movimiento posible, lo que conllevará la reducción de los tiempos de trabajo.
En el diseño de la distribución deben estar perfectamente definidas las siguientes zonas:
A. Zonas de carga y descarga
B. Zona de recepción
C. Zona de almacenaje
D. Zona de preparación de pedidos
E. Zona de expedición
Un ejemplo de un lay-out en el que se han tenido en cuenta todas estas áreas es éste:
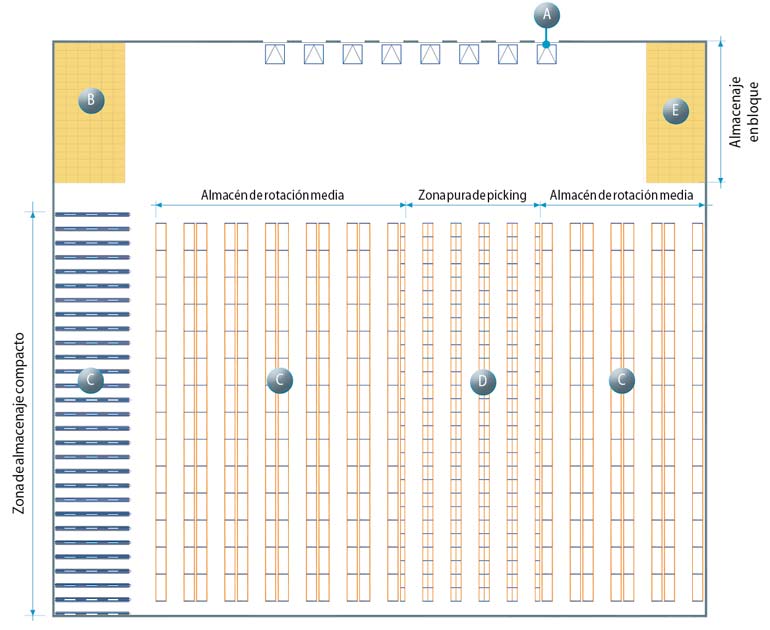
Zonas de carga y descarga (A)
Las zonas de carga y descarga, normalmente situadas en el exterior del almacén o combinadas con éste, son aquellas a las que tienen acceso directo los camiones o vehículos de transporte y reparto de mercancías.
En un almacén bien organizado es conveniente separar estas actividades del resto de la instalación, disponiendo, para ello, de espacio suficiente para la carga y descarga. Esta zona puede estar integrada en el almacén o ser independiente.
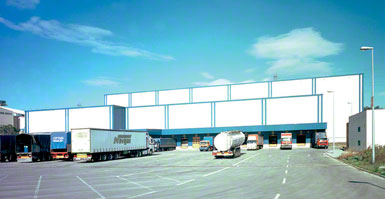
Muelle con andén adosado a un almacén..
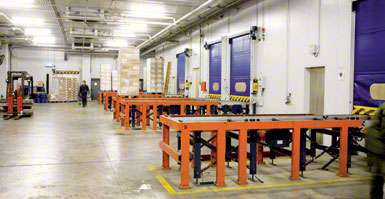
Muelle con andén intermedio en cámara frigorífica.
Zonas de carga y descarga integradas en el almacén
Si las áreas dedicadas a la carga y descarga están construidas directamente en los lados del almacén, de forma que el depósito y recogida de la mercancía se realiza sin necesidad de efectuar ningún tipo de rodeo, se dice que están integradas en la instalación. Su principal ventaja es una mayor velocidad en el manejo de la carga, por lo que su utilización es preferible a las opciones no integradas, siempre que se disponga del espacio suficiente para ello.
Los camiones son adosados al almacén por medio de muelles, que o bien pueden quedar separados del edificio por un andén o bien estar habilitados en éste con una puerta de acceso.
Los muelles separados con andén intermedio están indicados en aquellas situaciones en las que así se aconseje por la naturaleza de la mercancía, la conservación del medio ambiente interno o la seguridad del material almacenado.
Un ejemplo de aplicación característica de este tipo de muelles separados son las cámaras frigoríficas, en las que es necesario evitar, a toda costa, la pérdida de frío que podría ocasionar un muelle unido con una puerta de acceso. Sin embargo, hay otras muchas circunstancias en las que este diseño es preferible, especialmente en los que la seguridad del almacén pueda estar comprometida.
Los muelles unidos al edificio permiten que los camiones se acoplen directamente al muro del almacén. Para evitar modificar el ambiente interno de la instalación, sus puertas de acceso deben estar provistas, como mínimo, de un sistema de cierre hermético. Éste puede ser metálico o con fuelle de abrigo.
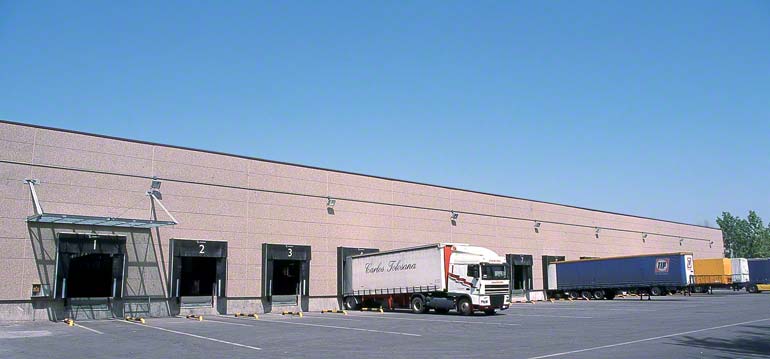
Muelles con acceso directo al interior del almacén.
Los accesos con cierre metálico están provistos de un sistema manual o automático que actúa sobre una barrera plana que puede ser fija, plegable o enrollable (como se ilustra). Se abre cuando se va a adosar un camión y se cierra cuando el vehículo ha terminado la operación. Si el sistema de cierre es automático, la conservación del ambiente interno es más efectiva.
Las puertas con fuelle de abrigo son aquellas que, además de estar provistas de cierre metálico, están dotadas de un túnel que abraza el camión cuando éste se acopla a la entrada, de tal manera que el ambiente interno se ve menos afectado por el externo.
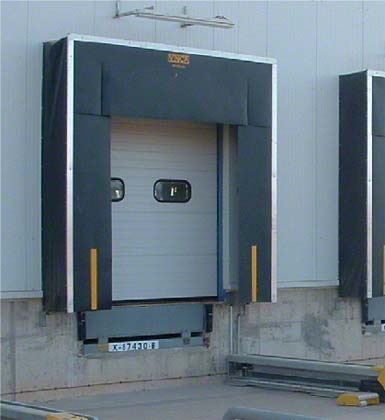
Puerta con fuelle de abrigo.
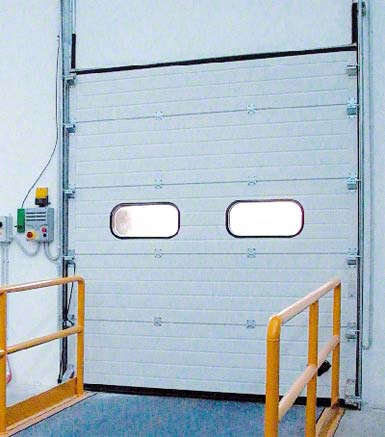
Puerta seccional.
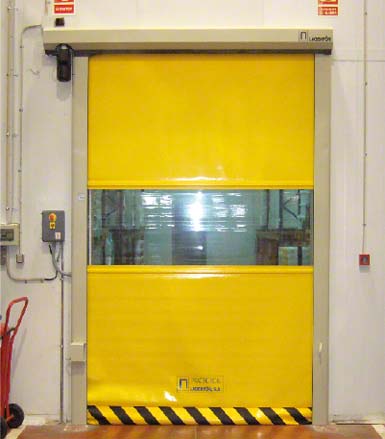
Puerta enrollable.
Cuando se diseñan este tipo de zonas de carga, es aconsejable plantear que el suelo del almacén quede elevado por encima del nivel de circulación de los camiones. También se pueden diseñar zonas de carga y descarga en las que los camiones se introducen en un foso, pero el movimiento y las operaciones se ejecutan con mayor celeridad si el almacén se halla más elevado.
La diferencia de nivel se puede lograr de diversas formas, por lo que no es imprescindible colocar la planta del edificio a una mayor altura. Por ejemplo, se puede llevar a cabo una reducción general de la zona de circulación de camiones, creando así un descenso progresivo que evite las rampas pronunciadas, que son, en definitiva, las que dificultan las maniobras y retardan el movimiento.
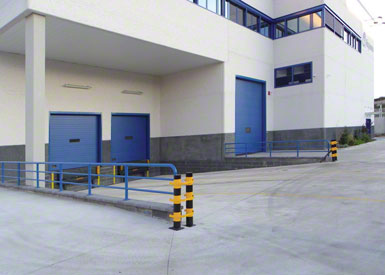
Vista de un muelle en foso.
A la hora de fijar esta diferencia de nivel, se pueden producir dos circunstancias, en función de si los camiones que van a acceder a las zonas de carga y descarga son propios o ajenos.
Si a las zonas de carga y descarga siempre van a acceder única y exclusivamente camiones propios, con una altura de caja exactamente igual en todos los casos, se puede fijar con precisión la diferencia de nivel sin necesitar nada más.
Cuando, por el contrario, los camiones que van a acceder a estas zonas son ajenos, de distintos orígenes y por lo tanto con diversas alturas de caja, se precisa la instalación de algún sistema que ajuste la diferencia de nivel.
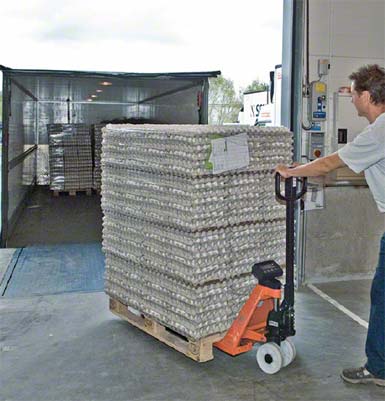
Transpalet.
En general, es imprescindible disponer de algún sistema de ajuste, porque incluso cuando se usa una flota propia, en la que en teoría no existe diferencia de altura entre los vehículos y el muelle, en la práctica ésta siempre existe.
Una de las razones de que esto suceda es que las ballestas de los camiones van cediendo con el paso del tiempo, bien porque con diferente carga la altura varía o, lo que es más habitual, porque la evolución de la compañía obliga a la adquisición o alquiler de otros transportes. En definitiva, la diversidad de alturas en las cajas de los vehículos es prácticamente inevitable.
Para salvar estas diferencias de nivel se pueden utilizar medios mecánicos o hidráulicos. Los primeros están basados en la utilización de puentes o pasarelas, normalmente metálicos, que se colocan de forma manual entre el muelle y el camión. La finalidad de estos elementos es que las carretillas elevadoras, transpalets o cualquiera de los otros medios mecánicos que se utilizan para la carga y descarga de camiones, puedan entrar y salir del vehículo.
Otra opción es el uso del segundo sistema que se ha citado y que está constituido por una plataforma metálica, dotada de uno o más cilindros hidráulicos. Este elemento facilita el acceso actuando de rampa –cuando está integrado en el propio muelle– o eleva y baja el camión. En la imagen se ilustra la segunda opción, con la plataforma integrada en el muelle.
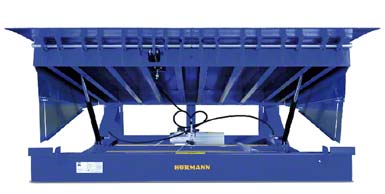
Plataforma individual.
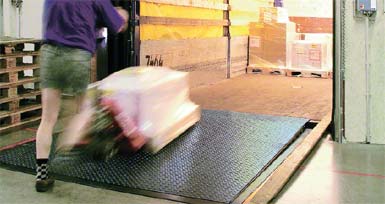
Plataforma integrada.
Zonas de carga y descarga independientes
Este tipo de áreas están localizadas fuera del almacén, aunque siempre dentro de su entorno (su terreno, se podría decir). Son llamadas así porque su funcionamiento es totalmente independiente del almacén propiamente dicho. Normalmente están formadas por una gran explanada a la que los camiones tienen acceso directo. Los vehículos se sitúan de tal manera que puedan ser cargados o descargados mediante el empleo de carretillas elevadoras.
Esta modalidad es utilizada preferentemente en aquellos almacenes en los que sólo se realiza una de las dos funciones, es decir, o sólo se carga o sólo se descarga mercancía. Esta peculiaridad permite conseguir la velocidad de manejo necesaria, ya que el no tener que adosar los camiones a los muelles, el tiempo empleado en la colocación de los mismos se reduce. Además, de este modo, el proceso de carga y descarga de la mercancía es totalmente independiente del ciclo de trabajo del propio almacén.
En estas zonas, las operaciones de manipulación de la mercancía en los camiones se pueden realizar por el lateral del vehículo o por su parte trasera. Si se lleva a cabo por el lateral, se utilizan carretillas elevadoras, tal y como se ilustra en la imagen de la izquierda:
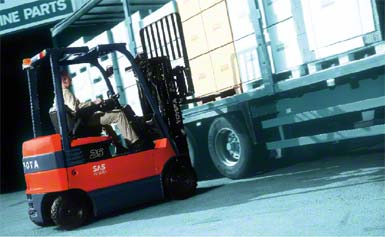
Carretilla manipulando la mercancía lateralmente.
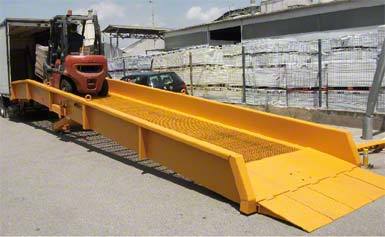
Acceso mediante rampa.
Si, por el contrario, la operación se efectúa por la parte trasera del camión se puede ejecutar de dos maneras distintas. La primera de ellas es acceder al camión con carretillas, mediante rampas. Éstas son, normalmente, metálicas y se adosan al camión, bien manualmente, bien mecánicamente. Existe una gran variedad de estos elementos en el mercado, aunque en la actualidad suelen emplearse dos, las rampas modulares y las adosadas a los muelles de descarga.
Las rampas modulares son estructuras metálicas provistas de una superficie de rodadura de tipo antideslizante, que puede ser fija –para situaciones en las que los camiones tengan la misma altura– o móvil para vehículos de diferentes alturas.
Por otra parte, las rampas adosadas a los muelles de descarga se habilitan mediante una obra de ladrillo u hormigón, que igualmente puede tener una altura fija o variable; en este último caso, su construcción es similar a la de los muelles de carga y descarga integrados que se han descrito anteriormente.
La segunda opción para realizar la carga o descarga de los camiones por su parte trasera es mediante deslizadoras mecánicas. Con este sistema no es necesario acceder al interior de la caja del vehículo para efectuar las operaciones, sino que se instalan unos carriles que permiten deslizar la mercancía a lo largo del interior del camión y el movimiento se lleva a cabo mediante el empuje de unas cargas sobre otras.
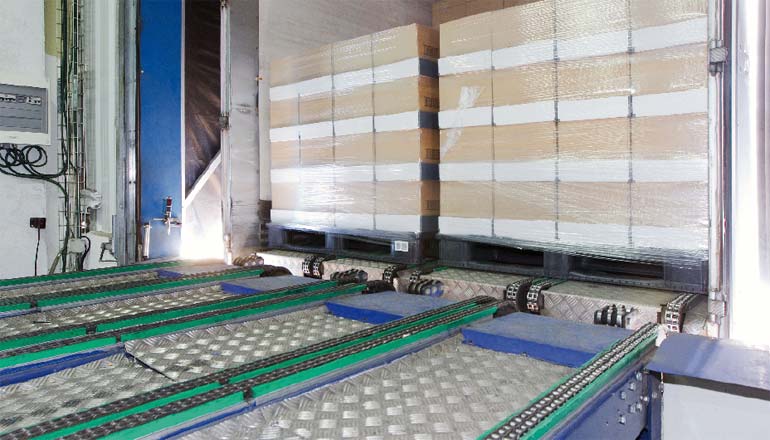
Carga automática mediante elementos deslizadores.
El proceso comienza con la colocación de una o varias unidades en la entrada del vehículo y éstas se empujan con una segunda tanda hasta llevarla a la posición que ocupaba la primera. De esta forma se van acumulando las cargas, una tras otra, hasta llenar la caja del camión.
Zona de recepción (B)
La zona de recepción debe estar situada de la manera más independiente posible del resto del almacén, con el fin de poder realizar en ella no sólo la recepción de la mercancía, sino también su control de calidad y su clasificación.
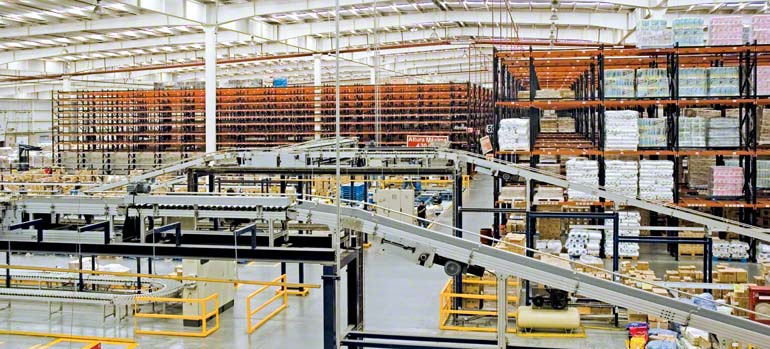
Zona de recepción
Una vez que se comprueba que el envío recibido responde a las características y calidad solicitada, se procede a la determinación de la ubicación de la carga dentro del almacén.
Dependiendo del tipo de almacén, puede ser que sea preciso o no realizar una labor de transformación de las unidades recibidas, en cuyo caso habrá que dimensionar esta zona adecuadamente para permitir esta función. Por ejemplo, puede ser necesario descomponer los palets que han entrado en unidades más pequeñas o extraer piezas que llegan flejadas, etc.
Dada la repercusión que puede tener una buena comprobación y, sobre todo, una correcta ubicación, en el rendimiento futuro del almacén, es preciso dotar a esta zona de la amplitud e independencia máximas posibles.
Actualmente, la práctica totalidad de los productos que se manejan en un almacén están provistos de códigos de barras que pueden ser leídos por un escáner. Así, una vez realizada la identificación de las unidades por parte del ordenador central del almacén, éste puede a su vez generar inmediatamente la etiqueta de ubicación de la mercancía. Esta etiqueta puede ser leída posteriormente por un operador de una carretilla elevadora o por los escáneres de los sistemas mecánicos automáticos que haya en el almacén para, en cualquiera de los dos casos, proceder a su colocación en donde corresponda.
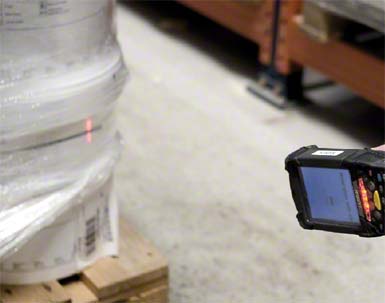
El terminal de radiofrecuencia lee la información codificada del palet.
Zona de almacenaje (C)
La zona de almacenaje, propiamente dicha, es aquella que está únicamente destinada a alojar mercancía. Existen diferentes tipos de almacenamiento de la mercancía: directamente en el suelo; directamente en el suelo, apilada y en bloques; o en las estanterías. El elegir una u otra forma dependerá sobre todo del tipo de producto que haya que almacenar, de su capacidad de apilado o de la cantidad y del tiempo que tenga que estar depositado.
El almacenamiento en pilas es aquel que se realiza colocando unas unidades de carga sobre otras sin más intermediación que el palet que les sirve de soporte. Presenta la ventaja de un mejor aprovechamiento del espacio, debido a que no se generan posiciones sin usar. No todos los materiales pueden ser almacenados así y se ha de tener en cuenta que, incluso aquellas mercancías que sí lo admiten tienen un límite de resistencia y, por lo tanto, una altura máxima de apilamiento. La gran desventaja de este sistema es que no permite ningún tipo de accesibilidad, de forma que para poder tomar cualquier carga es necesario desmontar previamente la pila que exista encima de ella.
El apilamiento se puede utilizar con dos tipos de carga principalmente, la de gran resistencia interna y la contenida en envases rígidos. Las mercancías de gran resistencia interna, tales como los ladrillos de cerámica, los bloques de hormigón, etc., permiten un almacenaje directo, a veces incluso sin necesidad de palet o cualquier otro sistema de soporte. Otras mercancías, como los piensos, cementos y áridos en general, que se almacenan en sacos, también permiten esta forma de alojar la carga, gracias a su resistencia a la compresión, aunque sí que precisan de palets u otros sistemas de soporte para manejarlos adecuadamente.
Los envases rígidos, como las cajas de cartón, de madera o de plástico, pueden ser apilados de esta forma sin problemas, si bien la rigidez y la resistencia de estos embalajes son los factores que determinarán la posibilidad de acumular más o menos unidades a mayor o menor altura.
Cuando la necesidad de almacenamiento en altura supera la capacidad de resistencia al apilado de las unidades de carga o cuando se precisa una mayor accesibilidad para obtener una mayor disponibilidad del producto, es necesario recurrir al uso de estanterías.
El almacenamiento en estanterías se realiza mediante la colocación de unas estructuras metálicas, que, básicamente, están formadas por bastidores y largueros debidamente arriostrados. Estos elementos conforman una estructura multicelular que genera unos huecos en donde se pueden depositar las unidades de carga. La configuración y disposición de las células (o alveolos) pueden variar para acomodarse a distintas operativas y necesidades de accesibilidad y acumulación de la carga, como ya se ha visto en el capítulo “Sistemas de almacenaje”.
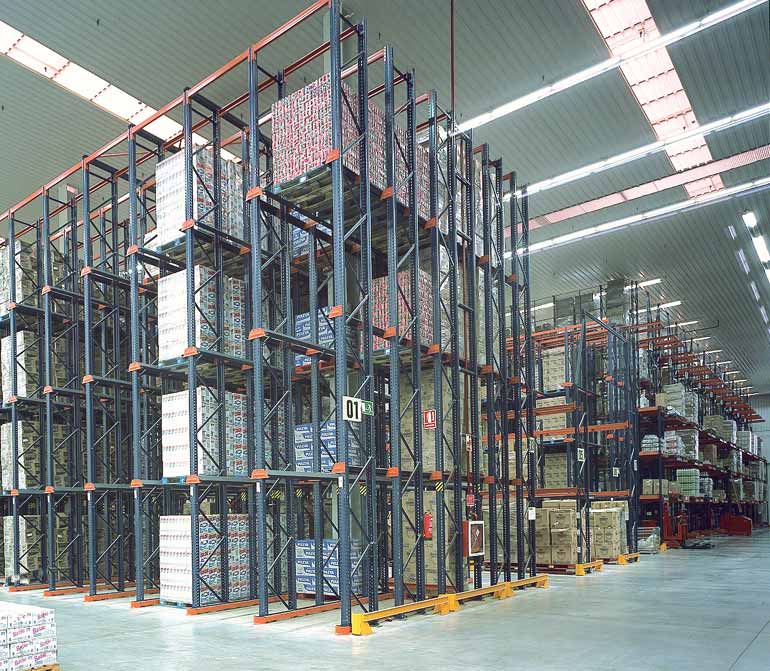
Almacén para una empresa de distribución.
Zonas de preparación de pedidos (D)
Estas áreas que se analizan ahora no son imprescindibles en todos los almacenes, tan sólo en aquellos en los que la mercancía de salida deba tener una configuración o composición diferente a aquella con la que entró o que requiera cualquier otra modificación.
Las zonas de preparación de pedidos pueden estar integradas en las de almacenaje. Tal es el caso del picking en estantería. También pueden quedar separadas de aquél, así como habilitarse en áreas específicas, generalmente dotadas de sistemas automáticos o semiautomáticos.
La imagen muestra la zona de preparación de pedidos de un almacén dedicado a la grifería y complementos para el baño.
Zonas de expedición (E)
Estas áreas están destinadas al embalaje de los pedidos preparados en las zonas que se han descrito en el punto anterior. Ya sea necesaria o no esa operación, esta zona puede estar destinada,también, a la acumulación de las mercancías que han de expedirse y que tendrán que cargarse en los vehículos de reparto o distribución.
Para una correcta velocidad de movimiento dentro del almacén, estos espacios deben diseñarse en un lugar específico y diferenciado del resto de la instalación.
Si se han habilitado zonas de recepción y expedición separadas, éstas deben disponer también de sendas zonas de carga y descarga. Por el contrario, si la recepción y la expedición están próximas, basta con habilitar un único espacio de carga y descarga, si bien esta opción supone una mayor dificultad de control del flujo de mercancías y del movimiento de vehículos.
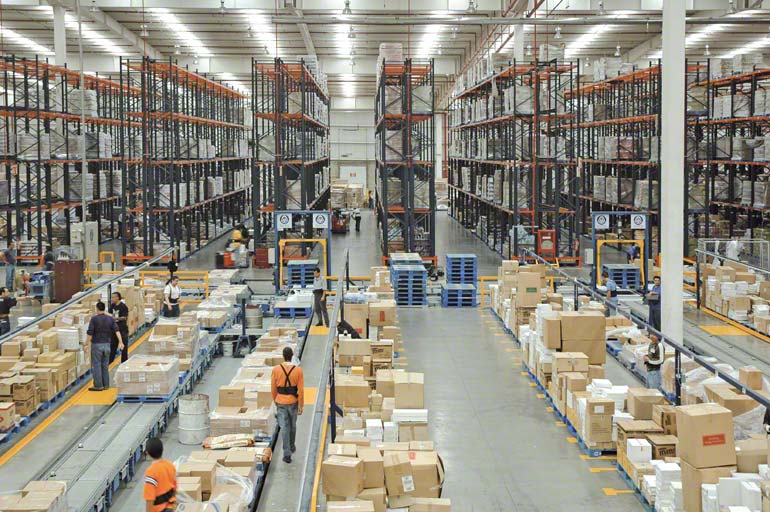
Almacén para empresa de distribución.
Zonas de servicios
Una parte del almacén debe destinarse a algunas actividades que forman parte de los servicios de la instalación, tales como las oficinas generales y la de control, los vestuarios, aseos y la carga de baterías de las máquinas de manutención.
Lo ideal es que la oficina de control esté situada en la zona de recepción y expedición y, a ser posible, entre las dos, con el objetivo de conseguir una mayor operatividad y eficiencia en el trabajo del personal dedicado a ello.
Los vestuarios, aseos y oficinas generales pueden estar en cualquier parte del almacén, aunque su ubicación más lógica es en las cercanías de las oficinas de control. Una buena solución para aproximar estos recursos es construir una entreplanta sobre la zona de recepción y expedición para instalar estas dependencias.
Por último, el espacio dedicado a la carga de las baterías de las máquinas de manutención debería estar aislado ydisponer de una buena ventilación, con el fin de conseguir una mayor seguridad y evitar así cualquier incidente en las operaciones que se lleven a cabo en esta área.
Cómo proyectar un almacén
Para proyectar un almacén es necesario recabar la mayor información posible sobre las necesidades del cliente, el espacio del que dispone y los medios con que cuenta. Esta recopilación de datos sólo está limitada por el nivel del proyecto al que se desee llegar en cada momento.
No basta sólo con saber lo que el cliente necesita o puede llevar a cabo, sino también es indispensable conocer las posibilidades que ofrece el mercado, para lo que se han de dominar los sistemas de almacenaje y estar al tanto de los equipos disponibles que se comercializan.
Veamos cómo se clasifican los datos que se recopilan. Cada uno de los factores influirá en la definición del almacén y todo ello, globalmente, repercutirá en su proyección.
Producto: ¿Cómo es la mercancía que se va a almacenar?
Qué datos son necesarios... |
¿Qué unidad o unidades de carga se emplean en la empresa? |
¿Cuáles son las dimensiones y peso de las unidades de carga? |
¿Qué cantidad de producto se pretende almacenar? |
¿Cuántas referencias o tipos de productos se van a ubicar? |
¿Cuál es la resistencia del producto a la compresión y deformación? |
¿El producto es sensible al clima? |
¿La mercancía es sensible al fuego? ¿Qué condiciones de seguridad ha de haber? |
¿Cuáles son los requisitos de rotación? |
¿Es necesaria una trazabilidad de las mercancías? |
¿Hay un maestro de artículos? |
¿Se prevé un crecimiento futuro? |
Estos datos determinan... |
El sistema de almacenaje que se empleará y las dimensiones necesarias de los huecos o estantes. |
El tamaño de la instalación, el sistema de ubicación y la distribución. |
Cómo deberá ser la manipulación y la resistencia de los equipos de almacenaje utilizados. |
Cómo será la operativa que se llevará a cabo. |
Qué zonas de trabajo se establecerán. |
Cómo se hará la distribución de los productos en la instalación. |
Cómo deberán ser los flujos internos. |
Si hay posibilidad de apilar el producto. |
Cuál es la estabilidad de la carga en su manipulación. |
Si hay posibilidad de desplomes (y, por lo tanto, si se necesita ocupar más espacio). |
Si será una instalación de temperatura controlada (almacén a temperatura negativa, refrigeración o temperatura ambiente). |
Cómo deberá ser el sistema contraincendios. |
Espacio: ¿Con qué infraestructura se puede contar?
Qué datos son necesarios... Para responder a estas cuestiones no es suficiente contar con un plano facilitado por el cliente, sino que se ha de ver el local para confirmar todos los datos y verificar las medidas. |
---|
¿Cómo es la forma y cuáles son las dimensiones del local? |
¿Hay características o limitaciones especiales relativas a accesos, suelos, ventanas, pilares, arquetas, instalaciones, líneas y conductos de energía? |
¿Hay espacios anexos al local que tengan alguna incidencia sobre él? |
¿Cuál es la resistencia del suelo? |
¿Cuál es la normativa constructiva de la zona? |
¿Es necesario realizar cálculos sísmicos? |
Estos datos determinan... |
La capacidad que podrá tener la instalación y cómo se realizará la distribución de mercancías en su interior. |
La accesibilidad disponible en el almacén. |
La distribución del espacio y la ubicación de salidas de emergencia. |
La necesidad de instalar estanterías con una resistencia adecuada. |
Equipos: ¿Cuáles son los medios disponibles?
Qué datos son necesarios... |
---|
¿Se cuenta con estanterías existentes? Si es así, ¿cuáles son sus medidas, cantidad y capacidad de carga? |
¿Se dispone de medios de elevación y transporte? En caso afirmativo, cuáles son sus medidas, su altura de elevación y su capacidad de carga. |
¿Se tienen ya elementos auxiliares, como cajas, paletas, etc.? ¿Cuáles son sus medidas y características? |
¿Hay una predisposición para adquirir nuevos equipos de almacenaje? |
Estos datos determinan... |
La necesidad de integrar nuevos equipos. |
Cuáles son las limitaciones de capacidad. |
Cómo se llevará a cabo una mejor adaptación a las necesidades del cliente. |
Si hay posibilidad de una mayor capacidad. |
Flujos y rotación: ¿Cómo circulan las mercancías?
Qué datos son necesarios... |
¿Cómo entrará el producto en la instalación, con qué frecuencia y en qué cantidad? |
¿Cómo se manipularán las mercancías? |
¿Cuál será la cantidad de pedidos y cuántas líneas contendrá cada pedido? |
¿En qué momento se preparará el pedido? |
¿Cómo saldrá el producto? Clasificación y cantidad. |
¿Cuáles serán las necesidades de rotación, cuarentena, etc., de la mercancía? |
Los productos se clasifican en... A: alta rotación B: media rotación C: baja rotación |
¿Cuáles son las necesidades actuales y cuáles las de crecimiento futuro? |
Estos datos determinan... |
El tamaño y distribución que deberá tener el almacén. |
Si es necesaria una reserva de espacios complementarios y cómo serán éstos. |
La distribución de las mercancías en las estanterías. |
La forma de preparar los pedidos. |
Si hay necesidad de medios auxiliares y cómo deberán ser. |
Cuál será el sistema de gestión empleado. |
Cuáles serán los medios de manutención y de qué tipo. |
Qué velocidad de operación y preparación tendrá la instalación. |
Personal: ¿Con qué profesionales cuenta?
Qué datos son necesarios... |
---|
Volumen de personal con el que se cuenta para trabajar en el almacén. |
¿Qué cualificación tiene el personal asignado a la instalación? |
¿Se trabaja en turnos? En caso afirmativo, ¿cómo están organizados? |
¿Qué predisposición hay a reducir o aumentar el número de personas y su cualificación? |
Estos datos determinan... |
Cuál será la capacidad de funcionamiento de la instalación. |
Si es necesaria o posible una mejora de la productividad. |
Si son precisos otros sistemas de almacenaje y equipos diferentes a los existentes. |
Qué medidas serán necesarias en lo relativo a los medios de manutención. |
Gestión y política empresarial: ¿Cómo se hacen las cosas?
Qué datos son necesarios... |
¿Cómo se lleva a cabo el control del almacén? |
¿Hay ya un Sistema de Gestión de Almacenes? (software SGA). |
¿Cuáles son los medios disponibles? |
¿Es necesario agilizar los pedidos? |
¿Es conveniente reducir el stock? |
¿Cuál es la importancia del prestigio para la empresa y en qué se basa? |
¿Hay potencial de inversión? |
¿Qué sistema de ubicación se utiliza? |
Estos datos determinan... |
Si será necesario mejorar el sistema de gestión. |
Cuál será el sistema de almacenaje y de preparación de pedidos más apropiado. |
Qué sistema de ubicación habrá que adoptar. |
Cuál será el espacio necesario. |
Qué cantidad de stock se podrá gestionar. |
Si será necesaria alguna reducción o aumento de personal. |
Cuál será el grado de efectividad de la instalación. |
Cómo se llevará a cabo la aplicación tanto de los sistemas, como de los medios disponibles. |
Y, en último término, el éxito o el fracaso de la solución desarrollada. |
El tipo de producto, el espacio donde irá almacenado y los equipos para su manutención serán, entre otros, condicionantes en el proyecto de todo almacén.
DISEÑO Y LAYOUT DE ALMACENES Y CENTROS DE DISTRIBUCIÓN
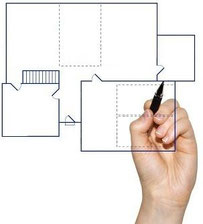
El papel de los almacenes en la cadena de abastecimientoha evolucionado de ser instalaciones dedicadas a almacenar a convertirse en centros enfocados al servicio y al soporte de la organización. Un almacén y un centro de distribución eficaz tiene un impacto fundamental en el éxito global de la cadena logística. Para ello este centro debe estar ubicado en el sitio óptimo, estar diseñado de acuerdo a la naturaleza y operaciones a realizar al producto, utilizar el equipamiento necesario y estar soportado por una organización y sistema de información adecuado.
Los objetivos del diseño, y layout de los almacenes son facilitar la rapidez de la preparación de los pedidos, la precisión de los mismos y la colocación más eficiente deexistencias, todos ellos en pro de conseguir potenciar las ventajas competitivas contempladas en el plan estratégico de la organización, regularmente consiguiendo ciclos de pedido más rápidos y con mejor servicio al cliente.
¿EN QUÉ SE DIFERENCIA UN ALMACÉN DE UN CENTRO DE DISTRIBUCIÓN?
La siguiente tabla nos muestra las diferencias existentes entre las principales características de un almacén y un centro de distribución.
ALMACÉN | CENTRO DE DISTRIBUCIÓN | |
Función principal | Gestiona el almacenaje y manipulación del inventario | Gestiona el flujo de los materiales |
“Cost Driver” Principal | Espacio e instalaciones | Mano de obra |
Ciclo de Pedido | Meses, semanas | Días, horas |
Actividades de Valor añadido | Puntuales | Forman parte intrínseca del proceso |
Expediciones | Bajo demanda del cliente | “Push Shipping” |
Rotación del inventario | 3, 6,12 | 24, 48, 96, 120 |
En un almacén el objetivo principal del mejoramiento se enfoca en la optimización del espacio y en dotar de medios de manipulación de cargas normalmente a gran altura y con volúmenes de trabajo medios. Mientras en un Centro de Distribución la optimización se enfoca en un rápido flujo de materiales y en la optimización de la mano de obra, sobre todo en las labores de Picking.
Sin embargo, se considera que la tipología del almacén influye decisivamente en el diseño de un Centro de Distribución, razón por la cual en este módulo se abordará el diseño y layout desde una perspectiva múltiple que contemple tanto a los Centros de Distribución, como a los almacenes, ya que si el objetivo fundamental del diseño de un Centro de Distribución consiste en la optimización del flujo de materiales, el almacén no está alejado de este contexto, dado que lo que aquí se pretende es abordar las pautas necesarias para la consecución de un Almacén óptimo.
¿QUÉ ES EL DISEÑO Y QUÉ ES EL LAYOUT DE UN ALMACÉN Y UN CENTRO DE DISTRIBUCIÓN?
Especialistas en logística (como es el caso del equipo de Pricewaterhousecoopers) han identificado dos fases fundamentales al momento de diseñar un almacén; estas son:
- Fase de diseño de la instalación. El continente
- Fase de diseño de la disposición de los elementos que deben "decorar" el almacén; el layout del almacén. El contenido
¿QÚE DEBE INCLUIR EL DISEÑO DE LAS INSTALACIONES?
El diseño de las instalaciones hace parte de los procesos estratégicos que debe ejecutar lagestión de almacenes, dicho diseño debe incluir:
- Número de plantas: preferentemente almacenes de una planta.
- Planta del almacén: diseño en vista de planta de la instalación.
- Instalaciones principales: Columnado, instalación eléctrica, ventilación, contra-incendios, seguridad, medio ambiente, eliminación de barreras arquitectónicas.
- Materiales: principalmente los suelos para lo cuales se debe tener presente la resistencia al movimiento de los equipos de manutención, la higiene y la seguridad.
¿QUÉ ES EL LAYOUT Y CUÁL ES SU OBJETIVO?
Como se describe en la segunda fase del diseño de almacenes, el layout corresponde a la disposición de los elementos dentro del almacén. El layout de un almacén debe asegurar el modo más eficiente para manejar los productos que en él se dispongan. Así, un almacén alimentado continuamente de existencias tendrá unos objetivos de layout y tecnológicos diferentes que otro almacén que inicialmente almacena materias primas para una empresa que trabaje bajo pedido. Cuando se realiza el layout de un almacén, se debe considerar la estrategia de entradas y salidas del almacén y el tipo de almacenamiento que es más efectivo, dadas las características de los productos, el método de transporte interno dentro del almacén, la rotación de los productos, el nivel de inventario a mantener, el embalaje y pautas propias de la preparación de pedidos.
MODELOS DE GESTIÓN SEGÚN LA ORGANIZACIÓN FÍSICA DE LOS ALMACENES Y CENTROS DE DISTRIBUCIÓN
Un óptimo diseño de las instalaciones de un almacén y un centro de distribución debe redundar en un adecuado flujo de materiales, minimización de costes, elevados niveles de servicio al cliente y óptimas condiciones de trabajo para los empleados.
Cuando la organización opta por ejercer la gestión física del almacén, se debe decidir acerca del modelo de gestión que se aplicará a nivel operativo, con base en su organización física. Según la organización física se consideran dos tipos de modelos de gestión operativa de los almacenes, estos son el Almacén Organizado y el Almacén Caótico.
GESTIÓN DEL ALMACÉN ORGANIZADO
Principio: Cada referencia tiene asignada una ubicación específica en almacén y cada ubicación tiene asignadas referencias específicas.
Características:
- Facilita la gestión manual del almacén
- Necesita preasignación de espacio (independientemente de existencias).

GESTIÓN DEL ALMACÉN CAÓTICO
Principio: No existen ubicaciones pre-asignadas. Los productos se almacenan según disponibilidad de espacio y/o criterio del almacenista.
Características:
- Dificulta el control manual del almacén
- Optimiza la utilización del espacio disponible en el almacén
- Acelera el almacenamiento de mercancías recibidas
- Requiere sistemas de información electrónicos

PRINCIPIOS DE LA DISTRIBUCIÓN DE ALMACENES
Existen una serie de principios que deben seguirse al momento de realizar la distribución en planta de un almacén, estos son:
- Los artículos de más movimiento deben ubicarse cerca de la salida para acortar el tiempo de desplazamiento.
- Los artículos pesados y difíciles de transportar deben localizarse de tal manera que minimicen el trabajo que se efectúa al desplazarlos y almacenarlos.
- Los espacios altos deben usarse para artículos predominantemente ligeros y protegidos.
- Los materiales inflamables y peligrosos o sensibles al agua y al sol pueden almacenarse en algún anexo, en el exterior del edificio del almacén.
- Deben dotarse de protecciones especiales a todos los artículos que lo requieran.
- Todos los elementos de seguridad y contra incendios deben estar situados adecuadamente en relación a los materiales almacenados.
ETAPAS DE LA DISTRIBUCIÓN FÍSICA DE UN ALMACÉN
La distribución física de un almacén puede dividirse en cinco etapas fundamentales, estas son:
- Determinar las ubicaciones de existencias y establecer el sistema de almacenamiento.
- Establecer el sistema de manejo de materiales.
- Mantener un sistema de control de inventarios.
- Establecer procedimientos para tramitar los pedidos.
- Seleccionar el medio de transporte.
DISEÑO EXTERNO DE ALMACENES Y CENTROS DE DISTRIBUCIÓN
EDIFICIOS Y ZONAS EXTERNAS

Cuando abordamos la infraestructura de un almacén o un centro de distribución (CEDI) es intrínseco el abordaje de aspectos claves como los son la seguridad y la productividad de las operaciones que en estos se efectuen. Tener la posibilidad de trabajar el diseño del edificio y las zonas externas del almacén o el CEDI partiendo de las necesidades logísticas de la organización es una ventaja vital, y al mismo tiempo una gran responsabilidad de gestión, dado que de las decisiones que se tomen al respecto dependerá el rendimiento de los tiempos que tardan en realizarse las operaciones de traslado y manipulación de unidades, la optimización de las condiciones de seguridad y el máximo aprovechamiento del espacio disponible.
El diseño externo del almacén y el CEDI abarca la orientación del edificio, la vías de acceso, muelles, andenes, plataformas, pasarelas, rampas, puertas, dimensiones del edificio destinado al almacenamiento (superficie, altura). Además, existen muchos factores de vanguardia logística a considerar, factores como el diseño de una infraestructura compatible con estrategias de reabastecimiento continuo, entregas paletizadas, cross docking y/o entregas certificadas.
Accesos y cerramientos
El diseño de accesos y cerramientos es un aspecto fundamental cuando se busca minimizar la interferencia entre los vehículos que participan del proceso de entrega y recogido desde y hacia el almacén o el CEDI, así como también busca minimizar la interferencia entre los medios de carga y descarga y el personal que transita por las vías de servicio. Para planificar de la mejor manera los accesos y cerramientos se debe tener en cuenta que:
- Los accesos en forma de "Y" son los que ofrecen mayores ventajas; los vehículos que entran en el almacén pueden abandonar rápidamente la carretera sin bloquear el tráfico; y los que salen pueden incorporarse al tráfico con mayor facilidad.
- La carretera de acceso directo al almacén deberá ser - preferentemente - de doble calzada, y su longitud no será inferior al doble del camión más largo.
- Las vías de servicio pueden ser dobles (de anchura superior a 8 metros) o simples (de anchura superior a 4 metros), siendo estas últimas las que permiten la circulación más segura.
- Las superficies de rodadura deben soportar el peso de los camiones (entre 25 y 70 toneladas), y grandes escarchas (bloques de hielo que la superficie debe soportar eventualmente) si las condiciones medioambientales dan lugar a ello.
- El tráfico debe ordenarse en el sentido contrario a las agujas del reloj, de esta manera la visibilidad del conductor (sentado al lado izquierdo) es mejor cuando maniobra y retrocede hacia los muelles.
- Las puertas de acceso tienen que ser independientes para peatones y para vehículos.
Muelles
Los muelles son plataformas de hormigón adosadas al almacén, cuyo propósito es que el suelo de este quede a la misma altura de la caja del camión. Antes de decidir dónde situarlos es necesario contemplar los siguientes factores:
- Utilización del almacén: Se debe realizar un estudio de los tipos de carga, la frecuencia de los ingresos, la necesidad de espacio para los camiones, etc. También se puede asignar las entredas que se pueden atender en cada muelle y destinar unos muelles para entradas JIT (Justo a Tiempo) y otras para el resto.
- Camiones de gran capacidad: La zona adyacente a los muelles debe ser de hormigón para evitar que los semiremolques se hundan cuando están separados de las cabezas tractoras y quedan suspendidos sobre las patas de apoyo. También se debe reservar una zona para aproximación, maniobra y aculatamiento de camiones grandes.
- Rampas y pendientes de acceso: Son necesarias para que las carretillas elevadoras puedan acceder a la zona de rodadura y al interior de los camiones, pero estas deben reducirse al mínimo en las zonas de los muelles. Para camiones de gran volumen es necesario contar con dispositivos especiales como muelles de regulación hidráulica o tijeras elevadoras instaladas en el suelo.
- Ubicación de los muelles: Según los expertos, la mejor ubicación de los muelles es en la calle lateral del edificio, lo cual permite un diseño funcional en forma de "U" , combinando así en una misma área la recepción y la expedición, permitiendo una mayor flexibilidad en la carga y la descarga de vehículos, dado que se puede dar una mayor utilización al personal y al equipo; sin embargo esta no es la única alternativa, también existen diseños en forma de "T" y en línea recta, cuya necesidad de aplicarlos la indicará el flujo de mercancías.
- Posición de camiones: La cantidad de muelles o posiciones de camión dependen del volumen de entregas, del tiempo que se requiere para efectuar las descargas y el traslado de las mercancías recibidas, además de los medios de manipulación existentes. El número de puestos debe ser igual al número máximo de camiones que cargan al mismo tiempo, considerando que los transportistas, generalmente hacen entregas en las horas de la mañana y las recogidas en la tarde. Un factor no menos importante a considerar es la posibilidad de expansión e instalación de muelles adicionales.
Zonas de Carga y Descarga
La ubicación de las zonas de carga y descarga está sumamente condicionada por la orientación del edificio y la distribución de los edificios colindantes. Si el almacén o CEDI se encuentra situado en una parcela con acceo desde varias calles, podemos diseñar zonas de carga y descarga en cualquiera de los frentes, pero si solo se cuenta con una entrada por una calle, la apertura será en una sola dirección. Un factor vital que influye en el diseño de las zonas de carga y descarga es el flujo deseado de mercancías, en este caso y según el flujo conveniente se puede optar por un diseño de zonas de carga y descarga que faciliten un flujo en "U", en "T" o en línea recta.
Según el medio de transporte que se utilice en el almacén o CEDI se deberá decidir si es conveniente que estas zonas de carga y descarga se encuentren ubicadas en el almacén o fuera de él (pero en su entorno), esta última alternativa es muy utilizada en plataformas logísticas y en centros integrados de mercancías, lugares donde predomina el transporte por buques, aviones o trenes.
DISEÑO INTERNO DE ALMACENES Y CENTROS DE DISTRIBUCIÓN (LAYOUT)

Efectuar la distribución del espacio interno de un almacén es un proceso sumamente complejo que requiere de superar las restricciones de espacio físico edificado y las necesidades proyectadas de almacenamiento (necesidades futuras de expansión). Las decisiones que desde la gestión de almacenes se tomen respecto a la distribución general deben satisfacer las necesidades de un sistema de almacenamiento que permita la consecución de los siguientes objetivos:
- Aprovechar eficientemente el espacio disponible
- Reducir al mínimo la manipulación de materiales.
- Facilitar el acceso a la unidad logística almacenada.
- Conseguir el máximo índice de rotación de la mercancía.
- Tener la máxima flexibilidad para la ubicación de productos.
- Facilitar el control de las cantidades almacenadas.
Estos objetivos nacen del reconocimiento de los siguientes siete principios básicos del flujo de materiales:
Principio | Descripción |
Unidad Máxima | Cuanto mayor sea la unidad de manipulación, menor número de movimientos se deberá de realizar, y, por tanto, menor será la mano de obra empleada. |
Recorrido Mínimo | Cuanto menor sea la distancia, menor será el tiempo del movimiento, y, por tanto, menor será la mano de obra empleada. En caso de instalaciones automáticas, menor será la inversión a realizar. |
Espacio Mínimo | Cuanto menor sea el espacio requerido, menor será el coste del suelo y menores serán los recorridos. |
Tiempo Mínimo | Cuanto menor sea el tiempo de las operaciones, menor es la mano de obra empleada y el lead time del proceso, y, por tanto, mayor es la capacidad de respuesta. |
Mínimo número de manipulaciones | Cada manipulación debe de añadir el máximo valor al producto o el mínimo de coste. Se deben de eliminar al máximo todas aquellas manipulaciones que no añadan valor al producto. |
Agrupación | Si conseguimos agrupar las actividades en conjuntos de artículos similares, mayor será la unidad de manipulación y, por tanto, mayor será la eficiencia obtenida. |
Balance de líneas | Todo proceso no equilibrado implica que existen recursos sobredimensionados, además de formar inventarios en curso elevados y, por tanto, costosos. |
Basado en recomendaciones de MECALUX
El layout de un almacén y de un CEDI debe evitar zonas y puntos de congestión, a la vez que debe facilitar las tareas de mantenimiento y poner los medios para obtener la mayor velocidad de movimiento; de esta forma se reduce por principio de flujo de materiales el tiempo de trabajo. La distribución interior de la planta del almacén se hace conjugando la conexión entre las distintas zonas del almacén con las puertas de acceso, los obstáculos arquitectónicos (pilares, columnas, escaleras, restricciones eléctricas, etc.), los pasillos y pasos de circulación (pasos seguros). Sin embargo, los factores de mayor influencia en la planificación de las zonas interiores son los medios de manipulación y las características de las mercancías, aunque vale la pena aclarar que:
"Los flujos de materiales deben condicionar el equipamiento a utilizar y nunca al contrario".
Por ello, antes de organizar los espacios se debe analizar las siguientes necesidades:
- Carga máxima de los medios de transporte externo, así como el equipo de transporte interno (carretillas, elevadoras, montacargas, grúas) y el tiempo necesario para cada operación.
- Características de las unidades a almacenar, tales como la forma, el peso, propiedades físicas.
- Cantidad que recibimos en suministro y frecuencia del mismo: diario, semanal, quincenal, mensual.
- Unidades máximas y mínimas a almacenar de cada una de las unidades, en función de las necesidades y la capacidad de almacenamiento.
En todo almacén y CEDI existen cuatro zonas que deben de estar perfectamente delimitadas, estas son: recepción, almacenaje, preparación de pedidos y expedición. Es muy común encontrar que estas zonas se subdividan en una o varias áreas en función de las actividades que se realicen, el volumen de la mercancía, del número de referencias, etc.
Distribución Interna del Almacén | |
Zona de recepción |
|
Zona de almacenamiento |
|
Zona de preparación de pedidos |
|
Zona de expedición o despacho |
|
Zonas auxiliares |
|
BASTIDAS, Edwin. Enfasis en logística y Cadena de Abastecimiento
DISTRIBUCIÓN EN PLANTA DEL FLUJO DE UNIDADES
Teniendo en cuenta las consideraciones anteriores respecto al flujo de materiales, se puede implementar una distribución del flujo de materiales en forma de "U", de "T" o en línea recta.
Distribución para un flujo en "U"
Entre sus principales ventajas podemos destacar:
- La unificación de muelles permite una mayor flexibilidad en la carga y descarga de vehículos, no sólo en cuanto a la utilización de las facilidades que tengan los referidos muelles, sino que a su vez permite utilizar el equipo y el personal de una forma más polivalente.
- Facilita el acondicionamiento ambiental de la nave, por constituir un elemento más estanco sin corrientes de aire.
- Da una mayor facilidad en la ampliación y/o adaptación de las instalaciones interiores.
Distribución para un flujo en línea recta
Las características más importantes se derivan precisamente de esa especialización de muelles; ya que uno se puede utilizar, por ejemplo, para la recepción de productos en camiones de gran tonelaje, tipo trailers, lo que obliga a unas características especiales en la instalación del referido muelles, mientras que otro puede ser simplemente una plataforma de distribución para vehículos ligeros (furgonetas), cuando se efectúa, por ejemplo, un reparto en plaza. Indudablemente este sistema limita la flexibilidad, obligando largo plazo a una división funcional tanto del personal como del equipo destinado a la carga y descarga de vehículos. El acondicionamiento ambiental suele ser más riguroso para evitar la formación de corrientes internas.
Distribución para un flujo en forma de "T"
Este layout es una variante del sistema en forma de U, apropiado cuando la nave se encuentra situada entre los viales, porque permite utilizar muelles independientes.
DIMENSIONAMIENTO DE UN ALMACÉN O CENTRO DE DISTRIBUCIÓN
Aunque el dimensionamiento forma parte del diseño e incide en el layout de un almacén y un Centro de Distribución, este tema será abordado en una página diferente debido a la longitud de esta página.
IDENTIFICACIÓN DE UBICACIONES

Tal como se mencionó en el módulo de Gestión de Almacenes, el manejo de la información sustenta la eficiencia y la efectividad de los flujos físicos. Por esta razón todas las zonas que componen el almacén o el CEDI deben de permanecer perfectamente identificadas (esta codificación debe ser conocida por todo el personal habilitado para entrar en el almacén). Las prácticas más comunes abordan la delimitación de las zonas por colores, o la presencia de carteles con la denominación de las zonas, ya sean colgados o posados en el suelo.
Toda ubicación que se encuentre en el almacén debe poseer su respectiva codificación (única) que la diferencie de las restantes. El método de codificación que se utilice es decisión propia de la empresa, ya que no existe un estándar de codificación perfecto para todas las empresas.
Las ubicaciones en la zona de almacenamiento pueden codificarse tanto porestantería como por pasillo.
- Codificación por estantería: Cada estantería tendrá asociada una codificación correlativa, del mismo modo que en cada una de ellas, sus bloques también estarán identificados con numeración correlativa, así como las alturas de la estantería, empezando por el nivel inferior y asignando números correlativos conforme se asciende en altura.
- Codificación por pasillo: En este caso, son los pasillos los que se codifican con números consecutivos. La profundidad de las estanterías se codifica con numeraciones de abajo hacia arriba, asignando números pares a la derecha e impares a la izquierda, y empezando por el extremo opuesto en el siguiente pasillo.
Identificación y trazabilidad de mercancías
Respecto a este tema visita: